Punctures are a fact of life for cyclists. Unpleasant but unavoidable, they’re a hated but accepted part of being a rider. At best, a puncture merely interrupts a ride; at worst it can end one. But for French tyre manufacturer Michelin, a puncture is what began its journey towards the globe-spanning, multi-billion-Euro company it has become today.
When a cyclist with a punctured tyre approached Éduoard and André Michelin at their rubber factory in Clermont-Ferrand in 1889, the brothers saw how difficult it was to repair and re-adhere the tyre to the bike’s wheel. The incident inspired them to come up with a better design for a bicycle tyre; one that could be removed, repaired and replaced more quickly.
Two years later, in 1891, Éduoard Michelin, filed a patent for the first detachable pneumatic tyre – the forerunner to today’s clinchers.
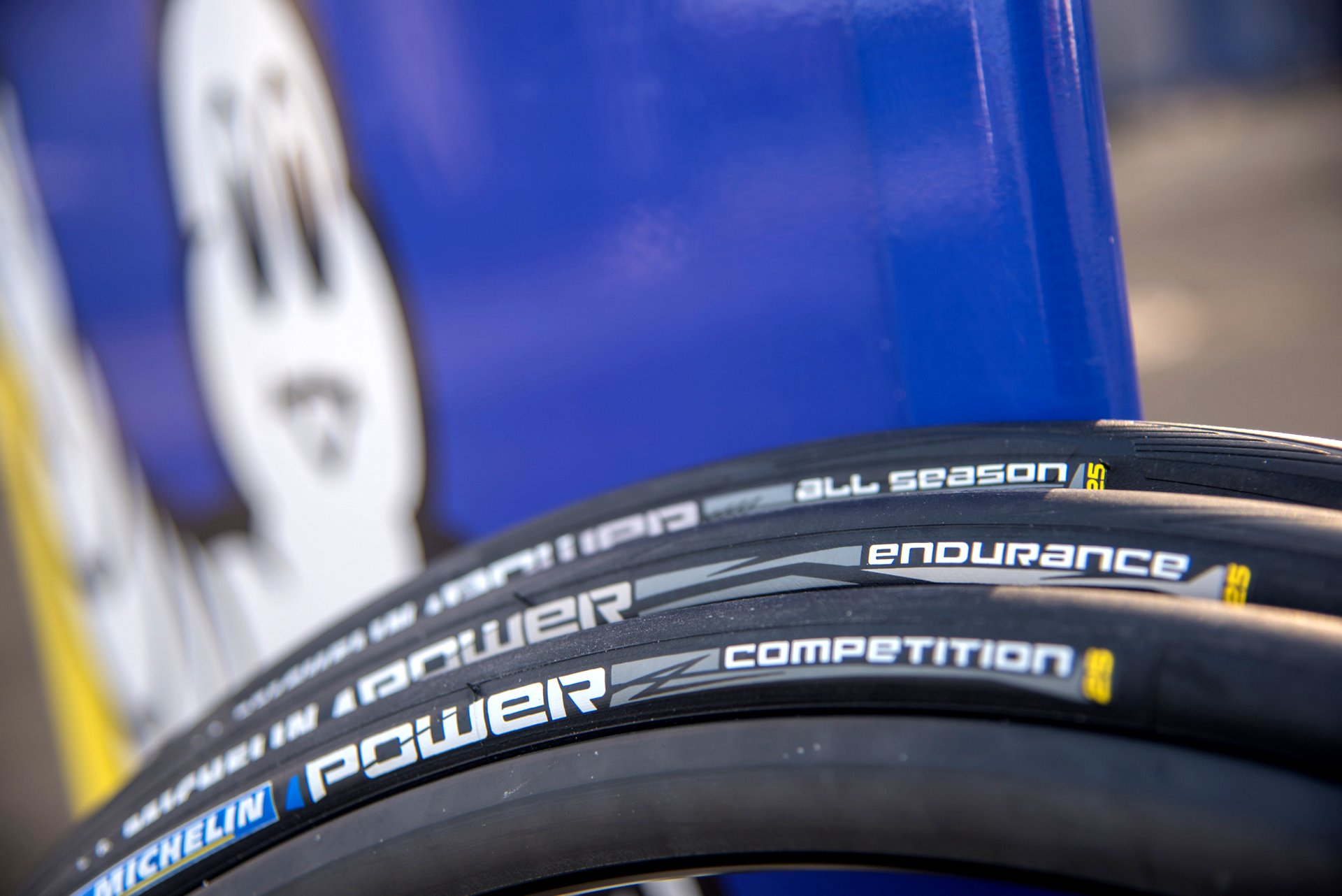
The brothers claimed their company’s design offered riders improved speed and efficiency since it allowed punctures to be repaired in a fraction of the time it took with existing tyres. To prove it, they gave a pair to Charles Terront to use for the first Paris-Brest-Paris race, a gruelling 1,196km event.
– The 14 tech innovations that changed road cycling –
Despite suffering punctures along the route, Terront rode – without sleep – to win in 71 hours and 22 minutes, finishing more than seven and a half hours ahead of his nearest rival.