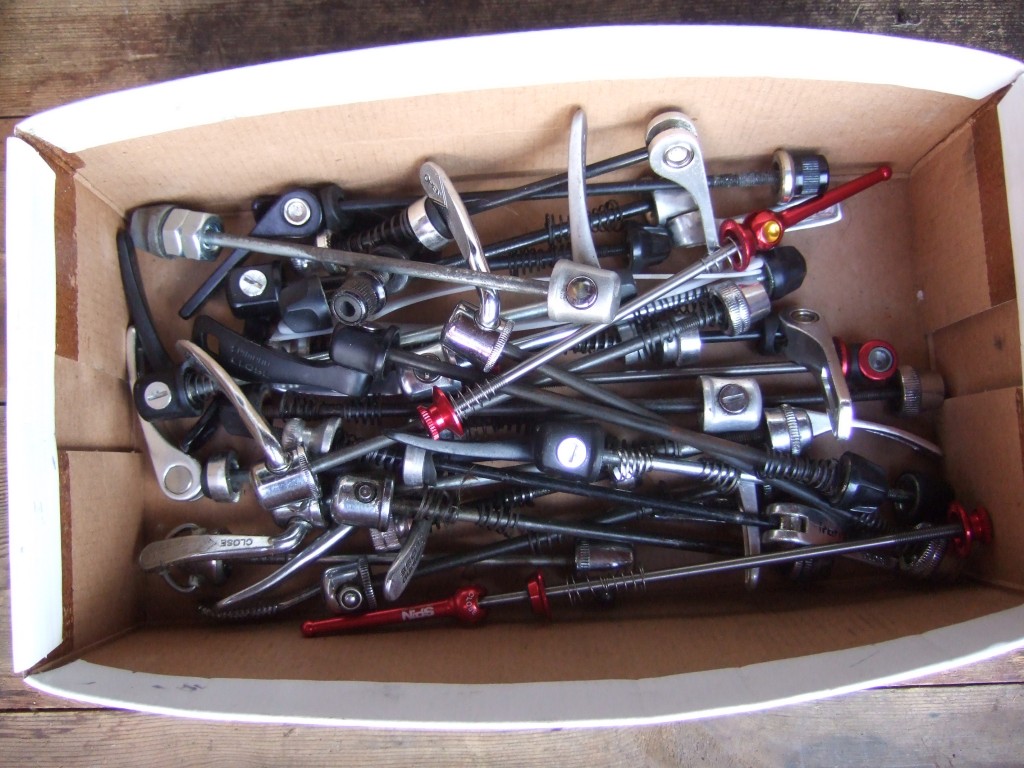
The quick-release skewer sitting inside a hollow wheel spindle was the invention that made Tullio Campagnolo’s name. The story goes that, on 4th November 1924 during the Gran Premio della Vittoria road race, he was halfway up the vicious climb of the Croce d’Aune in the Dolomites when he stopped in a snowstorm to turn his rear wheel around in order to access a lower gear ratio. Finding himself with frozen fingers and unable to slacken the wingnuts holding the wheel in place, Campagnolo is supposed to have uttered the words “Bisogna cambiar qualcossa de drio” – “something needs changing at the back” – before setting about changing it. The back of the bike, that is.
This fortunate event led to the invention and, in early 1930, patenting of the wheel retention system now universally adopted for performance lightweight cycles. The skewer, or rod, inside the spindle is only part of the system. It acts in tension, pulling the nut on one side and the lever head on the other up against the frame or fork dropouts and clamping them hard against the wheel bearing locknuts.
The system is actuated by a lever, which acts on an eccentric sited in the head. Flipping the lever through some 180degrees rotates the eccentric, moving it relative to the skewer head and thus either pushing the head against the dropout or moving it away. Sliding inside the spindle, the skewer itself transfers the movement to the nut on its other end. A thread on the skewer allows the nut to be adjusted to give fine control of the tightness of the lever – and of the point at which it begins to bite. Small springs keep the nut and head set equidistant from the faces of the dropouts to ensure quick and easy wheel fitment.
Alternative ways to tension the skewer involve the usually inferior concept of employing it as a very long, thin bolt, turning it by way of a lever acting as a wrench kept in situ; the need to turn the lever through several rotations to tighten it makes this process, which being in concept simpler than the eccentric must have occurred to Campagnolo, slower as well as requiring more space for the lever’s arc of operation.
Campagnolo’s original design placed the small-diameter eccentric on the shaft of the lever. Flipping the lever moves the centre point of the eccentric within the skewer shaft and keeps the moving surfaces away from contamination. Many low-cost designs of modern manufacture place the eccentric on the outside of the lever, where it presses against a seat on the face of the head. The moving surfaces are much larger in diameter and hence circumference, adding to friction, and are exposed to dirt and grit. Their action is inferior to that of a skewer with internal eccentric.
The skewer shaft is made in either high-tensile steel or titanium. The former is heavier – of course – and, since titanium has a lower Young’s modulus, also stiffer by a factor of two. Provided, that is, the steel and titanium shafts are of equal diameter. In practice, manufacturers of titanium skewers, perhaps looking to save as much weight as possible, compound the effect by making the shaft more slender still.
A typical example will have a shaft 4.5mm in diameter compared to the 5mm of a steel shaft. This gives the latter a cross-sectional area some 23percent greater which, added to the doubling of stiffness under tension of steel, obliges the titanium skewer to stretch around 46percent more to obtain the same clamping force. This, of course, comes from the degree of eccentricity of the eccentric and more of it requires more of a force applied to the lever. For this reason, steel skewers, especially if combined with an internal eccentric, give a much lighter action when being closed.
It is a mistake to try to obtain massive clamping force from the skewer. The lever should start to bite turned just past 90degrees so that closing the action does not require great force at the lever. Start the bite too early and not only will the lever require excessive force but the wheel bearings may undergo unwanted side loadings as the spindle is compressed.
Until recently with the introduction of better materials it was easy to stretch a skewer shaft so that it would neck down and possibly snap under the high tension that can be applied by a small-diameter internal eccentric. But then, that ability was what made Campagnolo’s seminal design so effective; not only was it truly quick in action, but it was – and is – more secure than threaded spindle nuts. Especially ones with wings on them.