The desire to own something unique, something made by hand, with care, consideration, and attention to detail, tailored to one’s own needs and specification, is as common to lovers of bicycles as to connoisseurs of fine tailoring.
Unhappily for those hoping to compare their creations, the craftsmen responsible for cycling’s bespoke designs are not to be found in a single, central location like Saville Row, but instead practice their art in workshops scattered around the country and indeed the world. This month, for only the second time, a show in Bristol will bring the practitioners of this thriving trade together from across the globe, allowing would-be owners to consider their wares in a single location.
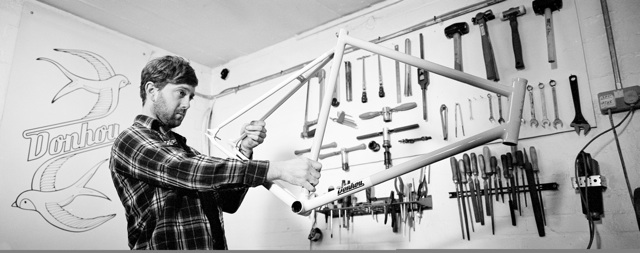
One man with good reason to make a second journey from Norwich to Bristol is Tom Donhou, winner of the ‘best in show’ award at last year’s celebration of bespoke bicycle manufacture.
Donhou discovered his calling as a bike builder during a two-wheeled odyssey that had taken him to Mongolia and across the Gobi desert, through China, the Himalayas and south east Asia to Singapore. Returning from his travels nearly two years ago, he began at once the work that has brought him a thriving business producing around twenty frames a year. “I had had a lot of time to think and I was designing and planning while riding. I see Donhou Bicycles as the same journey. It’s just changed shape a little. As soon as my plane had touched down from Singapore, I was trying to find ways to make it happen. It was a case of finding a workshop, calling in a few favours and working out what Donhou is. Getting a head badge sorted was an important step,” he says.

A background in product design and a childhood spent on bicycles had prepared Donhou for his moment of clarity. His experiences in China decided his modus operandi. “I could have just designed some bikes and had batches made in Taiwan. I’d cycled through China, seeing the effects and pressure of globalisation and decided I didn’t want anything to do with that. I decided I was going to make all my bicycles by hand, myself,” he says.
An ethos of using locally sourced materials where practical to do so without sacrificing quality led Donhou to Reynolds. He builds using 631, 853, and stainless steels. A frame with a 931 rear triangle has just been completed. The primary consideration in his selection of material is the use to which the finished article will be put. Steady demand for road, touring, and town bikes has made steel his stock in trade.
“I’m not a massive “steel is real” kind of person; each material has its purpose, but for the kind of bikes I make, it’s the most suitable. If I was building bikes for riders in the Tour de France I’d use carbon; I’m not. I’m building bikes that are used everyday; bikes that will last a life time. I use mostly Reynolds tubing: 631, 853 and also stainless steels. I’ve just finished building a frame with a 931 rear end. A lot of what I do is road bikes, tourers, and town bikes, but people seem to come to me to draw on my design background if they have something special in their mind,” he says. A handmade gear shifter for an eight-speed Shimano Alfine hub is a case in point. Work has begun on this singular item, but Donhou has yet to decide where to mount it.
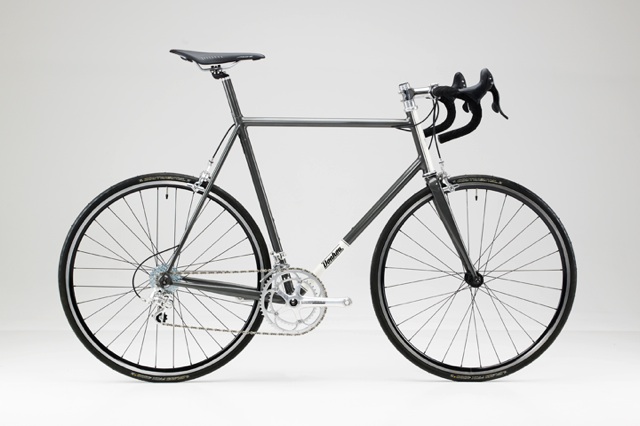
Discounting a frame made while at school, Donhou identifies his first bespoke creation as a track frame, made with lugs from Reynolds 853 and built to replace a stolen machine. “There’s so much to think about when designing and building a frame, so many variables, everything effects everything else. I can’t remember how long it took me, a fair while! There was a lot of fettling. Now it takes me less than half that time.”
While practice has reduced the production time, it would be wrong now to characterize the Donhou production process as swift. A current waiting time of four months, depending on the build, is evidence of an unhurried process where the end product is the principle concern.
“No two frames are the same, so you start from scratch each time. It’s the extra details that can really take the time though, designing custom dropouts, hand carving a bi-laminate construction. When you start throwing in things like custom bar and stem details, time can get away from you. I’m currently working on a handmade gear shifter for an eight speed Shimano Alfine hub. I’m not sure where it will be mounted yet. I’m working on it.”
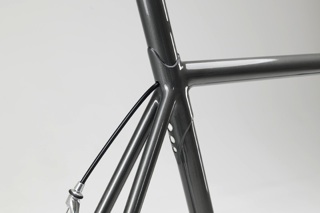
For a business trading in a traditional craft, Donhou’s marketing is decidedly modern. Followers on Twitter and Facebook and visitors to the website account for most of the firm’s customer base. Word of mouth and the press coverage that followed Donhou’s ‘best in show’ triumph at last year’s show have also helped. Some customers, however, prefer to see the machine in close-up before placing an order.
Donhou’s advice to would-be bike builders is simple: “I would say go for it. Don’t be afraid. Just fly at it. It’s the only way you’ll learn. There’s no better way to learn than by making mistakes.” And advice for those new to the craft? “Just be careful and take your time. Sleep on it if you need to.”
Bespoked Bristol will be held at Brunel’s Old Station from Friday March 23 to Sunday March 25.