Three-dimensional printing sprang into the public consciousness about six years ago, when photos of crudely-formed plastic shapes began emerging all over the internet. ‘This is the future of [insert type of object] manufacturing’, proclaimed the headlines.
At first these proclamations were mostly met with a raised eyebrow. And justifiably so. But as additive layering manufacturing, to give it its proper name, has developed, the equipment required to ‘3D print’ objects has increased in accuracy and precision, and dropped dramatically in price. Now, we’re starting to see the technology reach commercial viability in a whole range of fields, so could this also be the future of custom bike production?
3D printing, in very simple terms, involves designing an object with a computer programme and digitally splitting that design into extremely thin layers. The design is then interpreted by a 3D printing machine and built up, one wafer-thin layer at a time. The process is done with easily-melted materials like plastics, or titanium.
Inevitably the technology has been applied to bicycle production, just as it was to toilet roll-holders, cars and even firearms. Charge Bikes, based out of Frome in Somerset, were approached by the engineering team at Airbus, who wanted to find a way of demonstrating the commercial viability of 3D printing by manufacturing something that could be used in everyday life. Something far removed from the arcane mysteries of aviation. Something like a bicycle.
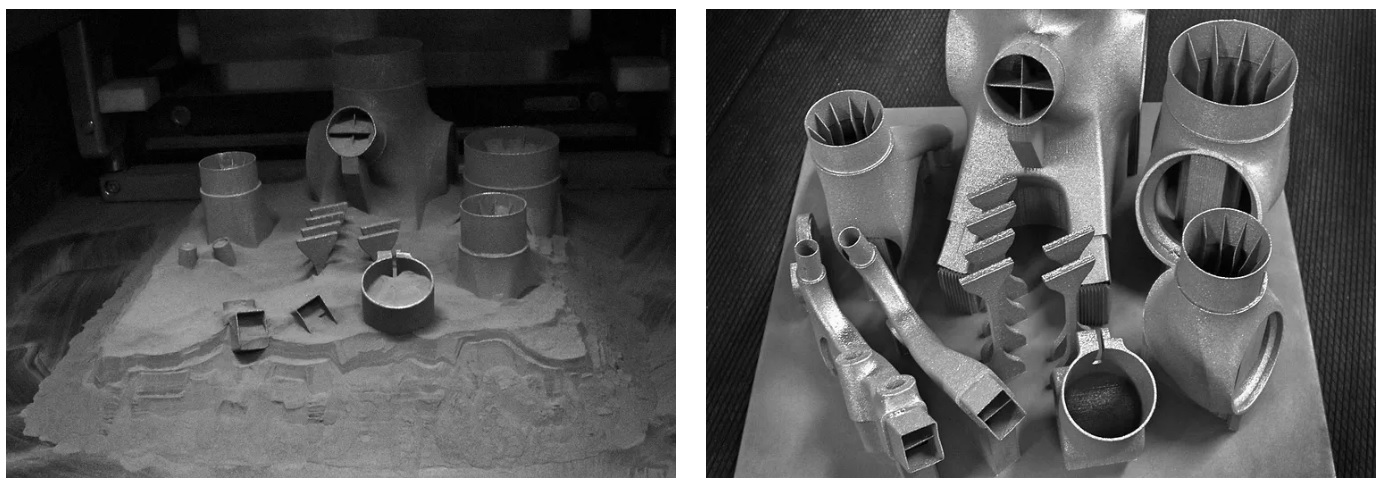