Titanium is a material that has enjoyed fluctuations in popularity but has become a firm favourite with cyclists more concerned by quality than fashion.
Briefly the choice of the peloton a decade and a half ago, before being swept aside by carbon, titanium remains the choice of select frame builders and customers who value its blend of strength, comfort, and lightness.
Mark Lynskey’s company specialises in the manufacture of titanium bicycles but he is at pains to stress that he does not view the business as “a titanium bike company”; rather, he says, titanium is the best material to use for a firm specialising in the manufacture of high-performance bikes.
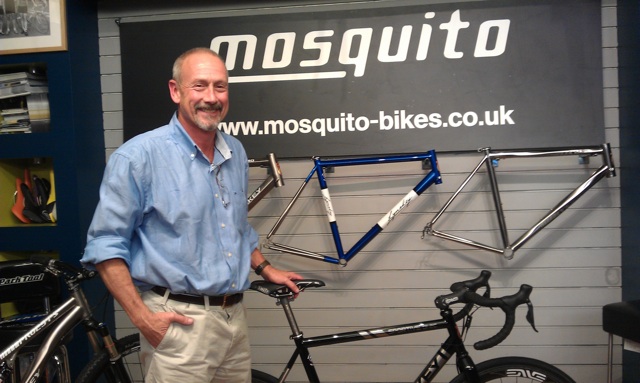
One of four brothers running the company, Mark Lynskey, who recently visisted London’s Mosquito Bikes, grew up in a family of engineers, his father the proprietor of a small machine workshop in Chattanooga, Tennessee, where the family business remains. Their experience in the aerospace industry drew them to titanium when they turned to making bicycle frames, a material Lynskey says is without equal for high-stress (as distinct from high temperature) applications, and in striking a balance between lightness, strength, and durability.
“From our very neutral perspective getting into this, we thought we need to use titanium,” he says.
Engineering has been a life time’s occupation for Lynskey, one begun at the age of eight, standing on milk crates in his father’s machine shop, running thread machines. “I can close my eyes right now and see that specifically,” he says. In 1962, Chattanooga was the ninth largest industrial centre in the USA, and little more than 100 miles from NASA’s base at Huntsville, Alabama, Lynskey recalls. “There was a whole cornucopia of other businesses down there and what my father’s business evolved into was exotic metals machining and fabrication.” Perhaps significantly for the direction taken by Litespeed, and later by Lynskey Performance Designs, Lynskey senior’s business had no extensive involvement with composites or the moulding of carbon fibre.
Necessity is the mother of invention, and necessity arrived at the Lynskeys’ door when David Lynskey took up cycling after injury prevented him from continuing to run competitively. In 1986, making bicycle frames was a new experience.
“I have to laugh,” Lynskey recalls. “We thought: ‘how hard can this be?’
“I remember David standing out in the middle of the machine shop, and he had bought a frame building book: ‘How to Build a Bike Frame.’ I remember looking at a diagram and saying: ‘Oh, they call that a chain stay. They call that a top tube.’ We knew nothing about building a frame. We knew how to manufacture: how to cut, and mitre, and weld, to machine and all that stuff. We knew nothing about building a bike frame except the tid-bits that David had garnered from riding and racing.”
The Lynskeys entered a steep learning curve with an idiosyncratic creation for David with a geometry not present on any of the production models. “David is about 6 feet tall and rides a 59cm or 60cm frame. I think this was the only frame on the planet to have about four inches of toe clip overlap. We learned what toe-clip overlap was in the car park.”
It’s fair to say the Lynskey family has now mastered the art of frame building. From 1986, they sold their frames as Litespeed, before selling the business in 1999. In 2005, David and Mark, with brothers Tim and Chris, decided they would build frames again. Lynskey Performance Products opened for business on January 1 2006.
The Lynskey road range extends to racing, ‘sports’, triathlon, touring, urban, and cyclo-cross frames, as well as hard tail and full suspension mountain bikes, and while titanium no longer represents the leading edge of bicycle manufacture, the company is keenly aware of developments in the sport and the industry.
The enormous growth in the popularity of cyclo-cross in the USA in recent years is reflected in the inclusion of two cyclo-cross bikes in the Lynskey range: the Pro Cross and the Cooper CX, a machine Lynskey says most of his customers choose as a year-round bike, one on which they may compete in two or three cross races each year, but also use for commuting and other applications. “In America, that’s driving it as much as cross racing specifically, maybe even more.”
With increasing numbers of cross bikes now being produced with disc brakes, it seems a suitable juncture to raise the topic of disc brakes on road bikes, a development with all the inevitability of fate, but one that awaits sanction from the sport’s governing body, the UCI. What are Lynskey’s thoughts on the topic?
“My personal opinion of it is that disc brakes on road, once the component manufacturers get it dialed in, will in fact be better. I emphasise, when they get it dialed in. I don’t think you can take a mountain bike brake system, put it on a road bike and be happy, and not just from a weight perspective. On road bikes, we use brakes for speed modulation, not stopping; a very different braking philosophy from mountain biking. There will be very different valving ratios, rotor sizes, for road bikes as compared to mountain bikes.
Lynskey Performance Products, he says, adopts “a very neutral attitude”.
“Our attitude on stuff like this is, if we can do it, if it makes sense to us, if it’s economically feasible, if it’s safe, we’re going to do it. The good news about us being a small company is we can do it pretty quickly and efficiently.
“The other aspect of that, is that if there are companies of significance that are going to be making disc brakes for road, the SRAMs of this world, the Formulas, we’re going to make a bike that they can put it on.”
While cyclo-sportives are not the phenomenon in the USA that they are over here, the middle aged man in lycra is one Lynskey recognises as the typical customer for the Sports Series, a range tailored to riders perhaps returning to the sport as much for the pleasure of owning and riding what Lynskey terms a ‘high performance bicycle’ as competitive cycling. ‘Quickness issues’ are addressed at the wheelbase (“you’re not going to have trails where just anyone can sit up and take their hands off the bar”) and head tubes and bottom brackets will be less stiff than machines from the Pro Series (Lynskey draws a distinction between flex and ‘absorption’).
The rear triangle is the area of the fame on which Lynksey’s engineers focus their efforts for comfort. “For your front end comfort, the frame almost does nothing: it’s your tyre, it’s your wheel, it’s your fork, it’s your stem, and your handlebar,” says Lysnkey. “At the rear end, about 90 per cent of that plays into your seat stays, and so you can bring a tremendous amount of comfort or lack thereof depending on your methodology, and of course, working in tandem with the chain stays, that’s where we’ll give a little more emphasis on our sports bikes.”
He recognises that the aesthetics of the frame are as important to his customer as its technical considerations are to his engineers, and says that competitors who ‘deny that reality’ aren’t doing the best job possible in product development. Bullet points on weight and geometry provide a ‘laundry list’ to convince wives and friends why such a machine is required, he jokes, but aesthetics make a personal statement about the owner. The heavily sculpted Helix is perhaps the best example, a machine Lynskey admits is a ‘darn good bike’ and ‘checks off every box’ of our conversation. But it is far from the end. “Is there more down the road for us? Absolutely.”