Ten miles north of York, in a garage owned by his father-in-law, Ricky Feather practices the frame builder’s art.
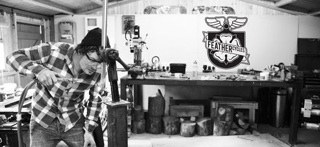
The exquisite hand carved lugs that decorate his frames, some mirror polished from stainless steel, are testament to the dedication with which he pursues his calling.
For it is a calling. Three years ago, Feather stood in New York City, surrounded by ‘absolutely gorgeous bikes everywhere’ in a world far removed from the Leeds factory in which he had fabricated ‘tiny parts for JCBs, trailers for articulated lorries and everything in between’ and decided he would earn a living by crafting frames.
His customers now seek him out, some visiting the garage in Easingwold, North Yorkshire to meet the man, drink tea, and ride their existing machines in front of him so he can see ‘what needs to be changed’. Some travel from London. They may have seen one of Feather’s creations locked up in a street. Some have ridden alongside other customers, registered the quality of the cycle next to them, and enquired how such a machine might be obtained.
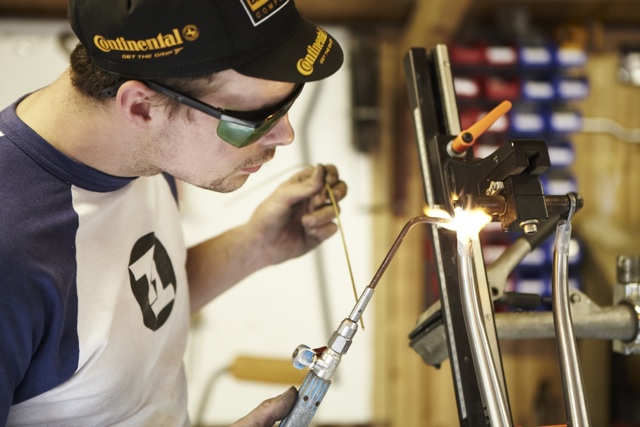
Feather doesn’t do short cuts, rush jobs, or cover ups. His more intricate designs can take up to 10 days to build; frames are photographed before they are painted so the customer can see the work that lies beneath the finish (“I’m a firm believer that paint hides everything”). His advice to anyone inspired to practice the frame builder’s art is simple: “You need a lot of drive, a lot of energy, a lot of dedication, and a lot of patience. If you haven’t got one of those things, you’re going to struggle. It literally has been my life for the last three years.”
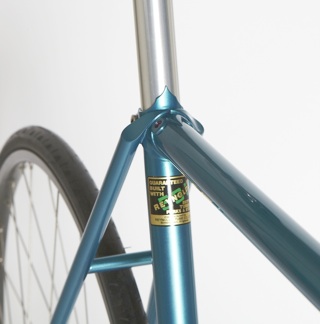
He works in steel. Reynolds and Columbus are his chosen suppliers. Many of his frames contain both: Reynolds for the main triangle, in some cases, with the rear triangle and fork blades fashioned from Columbus. The work is time consuming and demands patience; Feather made just 25 frames last year and expects to produce a similar quantity in 2012 – but perfection brings its own rewards. “I like to make sure every line is clear and crisp. If you’re doing a job with stainless lugs throughout, that can take forever. You see the time in the quality of the finish. It’s extremely satisfying when you see a lug go from a cast which is covered in pit marks to a mirror polished finish.”
Feather has recently finished a road bike to display at Bespoked Bristol, the handmade bike show that will bring 70 exhibitors and many more connoisseurs together at the city’s Brunel’s Old Station from March 23 to 25. The machine is an ‘all-rounder’ able to accommodate 25c tyres and mudguards, but built with shaped bridges “to get some nice lines flowing.”
The show is perhaps the clearest expression of a resurgence in the popularity of the hand built. “People are going back to their British roots. They want things hand built by craftsmen whether it’s bikes of furniture,” says Feather. “People like things that are built by hand rather than knocked up in a factory. I’ve no doubt that bikes made in a factory are high quality, but you don’t get that extra touch. People like something personal. They like that personal interaction with the builder.”
Entirely self-taught, Feather readily admits that the learning process is on-going. Older and wiser, he is proud of the ‘big steps’ Feather Cycles has taken in the last three years. The honing of his skills as a builder have progressed in smaller increments. “Pretty much everything I know about building a frame has been a long slow progression, you learn something new every day and think to yourself ‘how did I not think of that two years ago?’ In terms of actually building it has been mainly small steps.”
“I spend lots of time reading and researching. There were a lot of hours spent practicing before I built a bike. Now I am constantly chasing perfection.”